Путь российского инжиниринга
О медленном, но верном развороте в сторону локальных поставщиков решений для газохимии
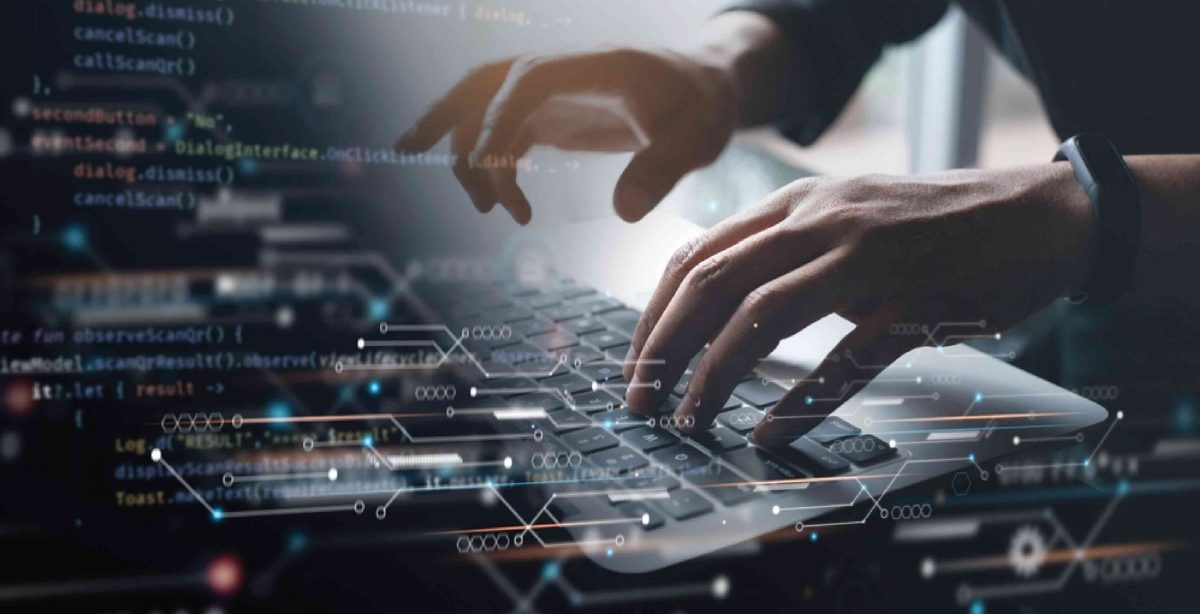
После ухода западных поставщиков компании из Китая получили карт-бланш — западных конкурентов как ветром сдуло, а к российским компаниям пока нет того безграничного доверия, которым ранее пользовались конкуренты из Европы и США. Сейчас в России наступил период затишья — достраиваются ранее начатые проекты, уточняются планы модернизации НПЗ по инвестсоглашениям, перестраивается работа установок на новые катализаторы. Все крупные проекты, как на Дальнем Востоке, так и в центральной части России достраивают китайские подрядчики на полных поставках с привлечением российских специалистов на точечные задачи. Поэтому сейчас можно говорить уже о практически 100-процентной зависимости российской газохимии от Китая.
Расцвет китайского инжиниринга
До февраля 2022 года западные технологические компании активно выстраивали отношения с крупнейшими российскими заказчиками — "Газпромом", "Новатэком", "Сибуром", "Еврохимом", "Щекиноазотом": по сути, со всеми, у кого на разных стадиях реализации шли крупные инвестиционные проекты. Здесь стоит упомянуть "Амурский газоперерабатывающий завод" ("Газпром") и строящийся в связке с ним "Амурский газохимический комплекс" ("Сибур" и Sinopec), Комплекс по переработке этансодержащего газа в Усть-Луге ("Газпром", "Русгаздобыча"), а также "ЕвроХим-Северо-Запад —2", комплекс аммиак/карбамид на площадке в Щекино, "Арктик СПГ-2" ("Новатэк").
Широкое русское гостеприимство и миллиардные инвестиции на эти проекты привлекали западных поставщиков технологий и оборудования — Linde PLC, Technip Energies, Topsoe, Maire Tecnimont Group, Axens и других не менее именитых компаний. Суммы контрактов исчислялись сотнями миллионов евро. Так, например, стоимость EPC-контракта с консорциумом немецкой Linde и турецкой Renaissance Heavy Industries на строительство газоперерабатывающего комплекса в рамках КПЭГ в Усть-Луге оценивалась в сумму около 5 млрд евро без учета СПГ-проекта. Еще один пример: контракт "ЕвроХима" с Maire Tecnimont Group на проектирование, материально-техническое обеспечение и строительство завода по производству аммиака в Кингисеппе подразумевал премию в 660 млн евро. Это были взаимовыгодные отношения, которые соединяли, как тогда казалось, надежных поставщиков и довольных заказчиков.
Однако, как показала практика, ситуация кардинально изменилась: поставщики оказались не такими уж надежными, несмотря на контрактные обязательства, а заказчики столкнулись с необходимостью изменения конфигураций проектов и поиска новых подрядчиков, удорожанием смет и сдвигом вправо сроков их реализации.
Подрядчики из Китая и ранее активно привлекались в российские проекты, а после февраля 2022 года это стало мейнстримом. Особняком тут стоит компания China National Chemical Engineering Co, Ltd (CNCEC), реализующая, на данный момент, по грубым оценкам, до 80% крупных проектов, передаваемых китайским подрядчикам в России.
"Щекиноазот" в 2019 году выбрал эту компанию для строительства комплекса аммиак/карбамид. Тем не менее, поставщиками технологий были Topsoe и Stamicarbon, а в 2023 году "Лукойл" привлек дочернюю компанию CNCEC — СС7 — для строительства газохимического комплекса в Буденновске. При этом несмотря на то, что в CNCEC входит много различных проектных институтов и строительных компаний, ей просто необходимо привлекать к работе российские проектные институты для того, чтобы разрабатывать и оформлять документацию в соответствии с нормами и требованиями российских регуляторов в области госэкспертиз и промышленной безопасности.
Путь российского инжиниринга
Предпочтение в реализации крупных проектов пока не отдается российским подрядчикам по нескольким причинам: дефицит квалифицированных кадров, способных закрывать такие большие объемы работ, отсутствие референсов и опыта реализации крупных проектов — это влечет дополнительные риски для заказчика.
Но есть и положительный опыт, например, на объектах "Газпрома" в строительство трубопроводной сети вовлекаются российские компании, в нефтепереработке — компания "Юникс" выступает генподрядчиком с расширенными функциями (по принципу EPC-контракта) на выполнение полного цикла работ по строительству третьей очереди Яйского НПЗ. Проект подразумевает ввод в эксплуатацию Комплекса депарафинизации дизельного топлива, мощностью 2,6 млн тонн в год, и Комплекса установки замедленного коксования, мощностью 1,34 млн тонн в год. Но такие крупные проекты в активе российских подрядчиков скорее исключение, чем порядок вещей.
В самом начале проекта перед заказчиком встает выбор: самому подобрать технологическое решение и конфигурацию проекта, а затем и генподрядчика или заключить EPC-контракт с конкретной компанией и отдать ей все ключевые полномочия, получив гарантии по выводу этих установок на проектную мощность, на сроки реализации проекта, и, соответственно, последующую передачу уже запущенного объекта.
Что нужно сделать, чтобы окончательно развернуть заказчика в сторону российских инжиниринговых компаний и проектных институтов? Прежде всего, нужна комплексная поддержка со стороны государства в части внедрения российских технологических решений, реализации крупных капиталоемких инвестиционных проектов и производства оборудования.
Под комплексной поддержкой мы понимаем субсидирование части капитальных затрат или предложение более выгодных финансовых условий на российскую составляющую проектов, как в части проектирования, так и поставок оборудования и материалов. Надеемся на выход обновленной программы поддержки, где это будет учтено. Сейчас в рамках первой кластерной инвестиционной платформы (КИП) промышленные предприятия, реализующие инвестпроекты по приоритетным направлениям, могут претендовать на получение льготного финансирования. Эта программа ориентирована на привлечение технологий и ресурсов для производства той продукции, которая ранее импортировалась в больших объемах. Необходима новая аналогичная программа, которая будет направлена именно на поддержку российской доли в реализации проектов — технологий и оборудования. Чем выше доля отечественных поставщиков — тем выгоднее будет потенциальному инвестору.
Одним из вариантов повышения вовлеченности российских компаний в реализацию крупных проектов может стать более активное создание консорциумов с компаниями из дружественных стран — Китая, Турции и других. Это позволит нивелировать такой риск как дефицит квалифицированной рабочей силы в России, иностранные подрядчики могут привлекать свои ресурсы.
Стоит отметить, что уже сейчас многие инвесторы стали уделять больше внимания отечественным подрядчикам и оборудованию. И здесь важно партнерство технологической компании и поставщика оборудования, чтобы предлагаемое решение соответствовало как техническим параметрам, так и ожиданиям заказчика по выходу на проектную мощность.
Отдельно стоит отметить, что инжиниринговые компании не всегда участвуют в проекте. Например, замена оборудования без каких-то существенных изменений конструкции самого агрегата не требует проведения проектных инжиниринговых работ. Это практически выполнение конструкторской работы самого производителя, подтверждение работоспособности требуемой конструкции. Участие технологических компаний необходимо, если нужен пересчет позиций оборудования под новые параметры, увеличение мощности, изменения конструкции или срока службы оборудования. Именно здесь требуется надежный союз поставщиков. Как пример: мы реализуем проект по замене внутренних устройств колонны синтеза аммиака, выступая единым поставщиком проектной документации и комплекта оборудования. Само оборудование производят субподрядчики из российских и зарубежных предприятий. И уже сейчас можно сказать, что существенная часть этого оборудования успешно производится в России. То же самое можно сказать о статическом оборудовании: емкостях, колоннах, реакторах, теплообменниках.
Что касается динамического оборудования, то в России сейчас очень ограниченный круг крупных производителей, и они загружены заказами на несколько лет вперед. Для увеличения производства нужна существенная модернизация, а для этого — гарантированные и постоянные заказы. Поставщики оборудования не против расширять производственные мощности, но им важно понимание перспектив на ближайшие 5-7 лет для расчета финансовой модели предприятий.
Катализаторный переход
В публичном пространстве много говорится о необходимости развития собственных производств катализаторов и обретения независимости в этой области. Действительно, многие из процессов привязаны к каталитическим системам, которые в России не выпускаются. В газохимии наиболее критичной остается ситуация с обеспечением производств катализаторами предриформинга, синтеза аммиака и метанола, которые на сегодняшний день не производятся в России и предпосылок для быстрого изменения ситуации на данный момент нет. Азотная промышленность обеспечена катализаторами собственного производства лишь на 25%.
Для катализаторов высокотемпературной конверсии СО, среднетемпературной конверсии СО и низкотемпературной конверсии СО сохраняется высокая доля импорта катализаторов (свыше 90%). Чуть лучше обстоят дела с катализаторами парового риформинга природного газа, где доля загрузок российских катализаторов может достигать 20% от годовой потребности рынка. Относительно катализаторов секции сероочистки и метанирования оксидов углерода — более 60% рынка занимают отечественные катализаторы.
В катализаторах вторичного риформинга сохраняется близкая к стопроцентной зависимость от импортных катализаторов. На данный момент загрузки подобных отечественных катализаторов носят единичный характер. Для снижения доли импорта в среднесрочной перспективе компания "ТопТех" участвует в проекте разработки катализаторов вторичного риформинга и его более требовательного аналога – катализатора автотермического риформинга, в качестве технического консультанта. Сейчас проводятся их испытания.
Специфика катализаторов газохимии определяется длительным средним срок пробега одной партии (в среднем 4-5 лет в зависимости от типа катализатора), поэтому на данный момент можно говорить о том, что процесс перехода с западных катализаторов на их аналоги только начат поскольку с момента ухода западных компаний с российского рынка прошло всего три года.
Ситуация с обеспеченностью отечественными катализаторами разная, и каждый процесс необходимо рассматривать по отдельности, при этом в контексте применения катализаторов синтез-газа стоит отметить, например, что отечественный рынок по международным меркам очень невелик, и правильное соблюдение разумного баланса между импортом и собственным производством качественной продукции на сегодня выглядит наиболее правильным решением. При этом "ТопТех", несомненно, заинтересован в локальном производстве качественных катализаторов, поскольку от них напрямую зависит эффективность проектируемых нами технологических установок.
Референсы не заставят себя ждать
Заработать доверие заказчиков молодым компаниям, даже если в ее штате специалисты мирового уровня, очень непросто. При выборе технологии производства все хотят видеть успешные референсы. У нас в России сейчас особый случай — мировые поставщики ушли, на их место пришли либо китайские компании, где свои особенности технологий производства с учетом сырья, либо есть российские со своими испытанными, но достаточно возрастными технологиями, либо современными, но пока не реализованными "в железе".
При этом для последних сложно говорить о референсах, когда у нас не так много предприятий и не так много новых "живых" проектов, где можно внедрить ту или иную технологию по сравнению с тем же Китаем, с его несоизмеримым количеством действующих и новых установок.
Да, некоторые российские технологии пока могут не иметь референсов, но по заявленным характеристикам они не уступают, а в чем-то превосходят те, что нам предлагают сейчас дружественные страны, например, по удельным расходным нормам. Так, например, технология автотермического риформинга для получения синтез-газа, которую продвигает на российском рынке "ТопТех", позволяет снизить расход природного газа до 10% при производстве аммиака по сравнению с традиционным печным риформингом. И экономить до 500 млн рублей в год за счет сокращения затрат на сырье.
Заказчика можно понять, когда разговор заходит о возможных рисках, хотя необходимо отметить, что эти риски, существовали в работе и с западными компаниями. А некоторые из рисков были совершенно непрогнозируемые, но при этом материализовались. Я имею в виду дружный уход почти всех лицензиаров с нашего рынка в 2022 году, оставивших реализующие инвестиционные проекты заказчиков наедине с самими собой и в полной неопределенности.
Сейчас наша общая задача не допустить повторения подобного сценария и совместно создать независимую конкурентную технологическую базу внутри собственного рынка, убедить в надежности собственных предлагаемых решений, чем ТопТех активно занимается.
Можно сказать, что в данный момент отрасль проходит ренессанс активного выстраивания сотрудничества между заказчиками, развивающими собственные технологии локальными подрядчиками, а также правительственными структурами, чтобы найти устраивающие все стороны долгосрочные решения.
Рано или поздно этот процесс нормализуется, для чего, конечно, необходима политическая воля, как в ситуации с самолетами. Есть Boeing, есть Airbus, но нам нужно свое. Ведь в конечном итоге только при совместной работе, доверии и разумном разделении рисков и выгод от проектов мы сможем уже в среднесрочной перспективе прийти к технологическому суверенитету по наиболее критичным газохимическим процессам и продуктам.