"Атомные" композиты
Как Росатом обеспечивает российскую промышленность композитами — в интервью заместителя гендиректора, технического директора композитного дивизиона госкорпорации Юрия Свистунова
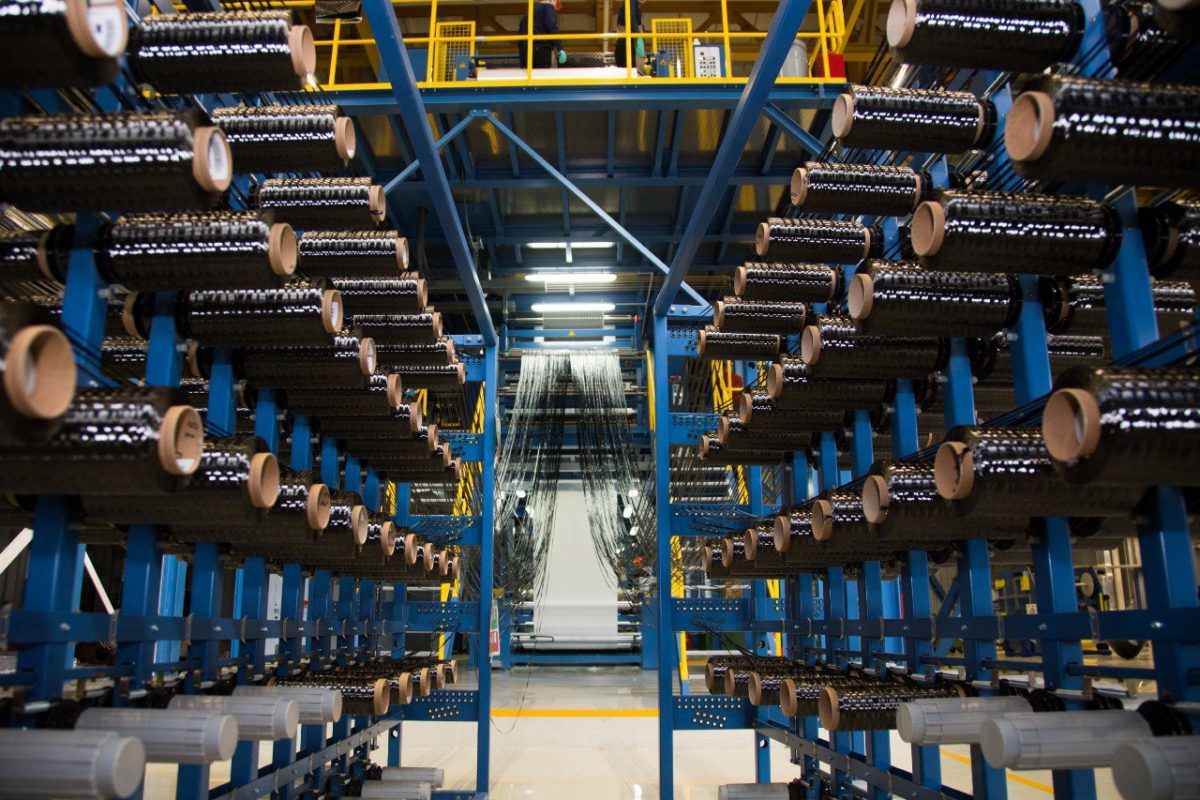
Производство и потребление композитных материалов в России сравнялось по объемам. В то же время российская промышленность уже сейчас готова вовлекать в свои проекты в области авиации, строительства, ветроэнергетики все больше инновационных материалов на основе углеродного и стекловолокна. Сегодня Росатом уже думает о том, как масштабировать производство, чтобы удовлетворить растущие потребности внутреннего рынка. О том, какие планы у Росатома по дальнейшему развитию отрасли — в интервью заместителя гендиректора, технического директора Композитного дивизиона Юрия Свистунова для портала ИнфоТЭК.
До 100%
– Композитный дивизион Росатома является крупнейшим производителем углеродного волокна в России. Какие тренды вы видите на этом рынке в текущее время?
– Композиты сегодня применяются почти повсеместно, рост производства и потребления — это тренд, который наблюдается не только в России, но и во всем мире. Негативные прогнозы по производству композитов на фоне сокращения программ по развитию авиации, к счастью, не реализовались. Глобальные темпы сохраняются и по разным оценкам потребление композитов в мире растет ежегодно на 11-13%.
В России происходит то же самое, что и в мире. Более того, если раньше считалось, что производители традиционных материалов, альтернативой для которых стали композиты, будут ограничивать рост рынка новых материалов, то сегодня мы видим, что такие производители, наоборот, запускают собственные проекты по разработке и производству композитных материалов, зачастую открывая новые сферы применения.
Мы знаем, что в нефтегазовой промышленности растет доля применения композитных труб, элементов инфраструктуры, в строительстве очень большие темпы роста применения композитов, особенно, когда речь идет об освоении сложнодоступных территорий, развитие которых без новых материалов невозможно. Конечно, такой позитивный тренд вселяет оптимизм.
Растущий спрос – это, разумеется, еще и вызов по его удовлетворению. Однако, у нас есть все необходимые компетенции и ресурсы для его удовлетворения, потому что мы занимаемся не только производством сырья, то есть волокон для композитов и связующих, но также работаем самостоятельно и в партнерстве на производстве конечных и промежуточных изделий, таких как препреги, ткани, направленные материалы.
– Каких производственных показателей удалось достичь в 2023 году? Полностью ли загружено производство?
– Начну с того, что единственный показатель, о котором можно говорить с уверенностью в таком конгломерате, как Композитный дивизион – это утилизация мощностей. В 2015 году, когда мы запустили завод по производству углеволокна, то начинали с показателя 40-50%. В то время, как у мировых лидеров считается нормой 80%, мы дошли почти до 100%. Конечно, такой уровень – это и показатель высокого спроса, но и вызов, требующий от нас расширять производство.
– Если говорить о заводе в Татарстане, то сколько он производит углеволокна в год?
– Сейчас объем производства находится на уровне 1000 т в год – это 100% загрузка. Мы выпускаем порядка десяти разных типов материалов, включая не только углеродное волокно, но и окисленное полиакрилонитрильное волокно. Мы постоянно работаем над тем, чтобы при стопроцентной загрузке оборудования повышать и эффективность производства, то есть давать в тоннах продукции больше. Мы ведем много проектов с нашими отраслевыми партнерами, работаем над сокращением затрат, постоянно технически развиваем производство.
Кратный рост
– Вы упомянули, что мировой рынок растет на более чем 10% в год, а российский рынок сопоставимыми темпами растет или опережающими? Как сейчас оцениваете?
– Фактически, по статистике последних трех лет, темпы именно такие, как я называл. Однако, в ближайшие два-три года они могут вырасти из-за того, что проекты в области гражданской авиации переходят к серийному производству. Мы видим прогнозы по выпуску самолетов, но здесь нужно помнить, что цикл самолетостроения очень длительный. Комплекты (особенно из композитов) производятся, конечно, заранее, поэтому уже сейчас мы видим не просто повышение спроса, а кратный рост объема задач в сфере авиации.
– Как вы видите горизонт до 2030 года или 2035-го года? Как будет развиваться тренд на композиты применительно к вашим проектам?
– Тренд на расширение применения композитов в краткосрочной перспективе потребует от нас смещения приоритетов в пользу стратегических отраслей, таких как авиационная и атомная промышленность. Я думаю, что доля подобных заказов вырастет в нашем портфеле с 30-40% до 80-90%. Как я говорил выше, мощности наши загружены полностью, поэтому нам придется выбирать на что их направить. Завтра нам нужно будет масштабировать производство, вводить новые мощности, потому что нам нужно удовлетворять рост спроса и в таких отраслях, как, например, строительство.
– Вы уже планируете строительство нового завода по углеволокну?
– Да, у нас такие проекты есть, есть несколько вариантов реализации. К сожалению, не могу сейчас подробно рассказать, но отмечу, что в наших планах увеличиться в несколько раз и по объему производства, и по объему выручки к 2030 году.
– В несколько раз – во сколько? В два-три раза?
– Будет зависеть от того варианта, который мы выберем.
Экспорт как проверка
– Есть ли у вас в структуре поставок экспортная составляющая?
– Да, но здесь стоит говорить об экспорте ради сохранения присутствия и конкурентоспособности на определенных рынках, в определенных нишах. Мы экспортировали много углеродного волокна в Китай, но сейчас другие приоритеты. Спрос на российском рынке огромный, за последние семь лет он вырос примерно в пять раз, и нужно удовлетворять в первую очередь его.
– И полностью закрываете потребности или все-таки российские переработчики вынуждены еще где-то искать варианты закупок?
– Согласно таможенной статистике сейчас в Россию импортируется определенный объем углеродного волокна.
– Можете ли оценить текущую потребность российского рынка в углеродном волокне?
– Я бы оценил потребность российского рынка в углеродном волокне на уровне 1000-1200 т, но это количество само по себе не говорит ничего. Наши клиенты почти не используют волокно в чистом виде, они применяют материал, который мы производим сами из собственного волокна.
Мы интегрированная компания – наше преимущество в том, что мы обладаем очень длинной цепочкой от самого раннего сырья в виде полиакрилонитрильного волокна до конечных изделий, и во второй трети этой цепочки находятся промежуточные продукты, которые производим в Москве и в Дубне. Мы создали производство препрегов, тканей и мультиаксиальных материалов.
Мы стремимся к тому, чтобы клиенты получали продукты более высоких стадий переработки, чем просто углеродное волокно.
– Вы сказали, что доля экспорта небольшая. Можете назвать, сколько процентов?
– Сегодня мы говорим, что на экспорт идет меньше 1%. Экспорт для нас был важен не только как источник заработка, но и возможность убедиться в том, что наша продукция является востребованной на высококонкурентном международном рынке. Мы эту стадию прошли, мы знаем, что наша продукция отвечает всем требованиям качества.
Растут направления российской промышленности, которым требуются наши продукты, растет востребованность композитов в целом и этот спрос нужно удовлетворить. Тот факт, что наши мощности полностью направлены на удовлетворение российского спроса – это положительный сигнал, который говорит и о росте национальной экономики и о том, что наше предложение востребовано в России.
Фокус на разработке технологий
– С учетом того, что вы планируете строительство новых мощностей, можно ли сказать о том, что вы ждёте бума спроса на углеволокно в ближайшие годы?
– Да, разумеется, мы ждем бума спроса, но это будет бум в понимании реалий композитной отрасли. Важно понимать, что особенность нашей сферы заключается в том, что разработка способов производства новых материалов и технологий их применения, квалификация материалов в таких сферах, как авиастроение, производство баллонов высокого давления, лопастей для ветроэнергетики и прочего занимает время. Резких скачков, роста на порядки в композитах не бывает.
Рост темпов потребления точно будет ускоряться. Я верю, что он будет на несколько процентов выше, чем та оценка, которую я в начале назвал, но происходить такой рост будет постепенно.
– Глава Росатома Алексей Лихачев говорил, что Россия вошла в четверку мировых композитных лидеров по углепластикам. Есть ли у вашего дивизиона стремление возглавить этот рейтинг стран, опередить США, Японию, Западную Европу по выпуску углеволокна и расширению сфер его применения?
– Наша компания с момента основания фокусировалась на лидерстве в разработке технологий и скорости их внедрения. Есть и другие подходы в композитах, которые мы наблюдаем сейчас, например, в Китае. Если относительно недавно там было мало производителей углеродного волокна, а в Индии, кстати, до сих пор нет ни одного, то сейчас по объемам производства волокна Китай сопоставим с величиной мирового рынка пяти-семилетней давности. Китайские производители заняты массовым выпуском стандартных типов углеродных волокон, многие не планируют развивать собственную цепочку производства или создавать новые продукты.
Наш фокус, наша философия противоположная – развитие технологий. Именно поэтому у нас такая длинная цепочка продуктов, в том числе в области сырья, номиналов — ПАН-прекурсоров и углеродного волокна, и материалов на основе углеродного волокна, и конечных изделий. Наше лидерство лежит в глубине компетенций: у нас есть и стандартные материалы, и специальные для узких и ответственных применений, где нельзя просто открыть каталог и выбрать какого-то производителя в мире, где, например, затребованы такие свойства, достижение которых занимает годы.
Мы боремся за мировое лидерство, развивая наши компетенции, каждый день.
– В текущем производстве вы используете только российские технологии или остались еще наработки импортных? Насколько мне известно, советские технологии производства углеволокна и сырья для него были утрачены, но вы попытались их реанимировать. Насколько успешно это все у вас получилось?
– Для производства в Татарстане мы разрабатывали все "с нуля". Технология производства углеродного волокна, как таковая, действительно, описана в учебниках, она известна, но она описывает общие подходы.
Особенность композитов заключается в том, что набор параметров для получения конкретного типа углеродного волокна требует своей технологии. Тот набор компетенций, который у нас есть в Татарстане, и в части прекурсора, и в части углеродного волокна – это результат нашей многолетней работы. Все технологии принадлежат нам.
Если говорить о наследии прошлого, у нас есть два завода — в Балаково и в Челябинске — где на базе тех разработок, которые велись еще в советское время, мы провели глубокую модернизацию и оборудования, и технологий, и подходов к производству. Сейчас эти производства работают наравне с новым предприятием в Татарстане, они поставляют материалы специальных применений. Называть их отстающими некорректно, это немного другие технологические подходы, другие типы волокон, но они сохраняют свою конкурентоспособность.
В Татарстане мы собираемся обеспечивать масштабирование и разрабатывать новый тип углеродных волокон. Никакой из типов углеродных волокон, которые мы сейчас выпускаем, не обременен лицензиями или ограничениями от сторонних компаний.
– Есть ли у вас запросы на коммерциализацию этих технологий? Хотите ли вы стать лицензиарами?
– В России мы пока не вели переговоры о том, чтобы создавать новые мощности вместе с кем-то на основе наших лицензий или продавать лицензию. Причина в том, что мы – единственный интегрированный производитель. Действительно, в прошлом у нас было несколько проектов, связанных с перспективами создания производства за рубежом, но мы все-таки сфокусировались на развитии производства по углеродному волокну только в России.
Своё оборудование
– А насколько сейчас ваши производства обеспечены российским оборудованием? Свои технологии — это замечательно, но у многих еще сложности возникают с оборудованием. Как у вас обстоит ситуация? Ведете ли вы собственные разработки в этом направлении?
– Да, мы запустили проект в позапрошлом году, создав компанию, которая станет основой для разработки отечественного оборудования, вся наша цепочка будет обеспечена специальным машиностроением. На российском рынке есть много возможностей для формулирования запросов на разработку нестандартного оборудования, но мы пришли к выводу, что ключевое оборудование для производства углеродного волокна мы должны разработать сами. Думаю, что по крайней мере какая-то часть наших производственных линий будет обеспечена отечественным оборудованием уже достаточно скоро.
– Какие годы вы ставите целью?
– Какие-то элементы линий мы начнем замещать уже скоро, определенную долю отечественного оборудования разработаем и поставим в рамках проектов, которые будут длиться со следующего года вплоть до 2027-2028 годов. Дальше будем наращивать долю вплоть до 100%.
– Правильно ли я понимаю, что сейчас в России у вас нет конкурентов, вы единственный производитель углеволокна и переработчик, да?
– У нас есть конкуренты, занятые в определенных отдельных частях жизненного цикла композита от сырья до конечного изделия. У нас есть конкуренты среди тех, кто делает конечные изделия, среди тех, кто делает ткани, препреги и материалы. Пока у нас нет конкурентов среди производителей углеродного волокна и среди производителей ПАН-прекурсора.
– Спрашиваю об этом, потому что у "Сибура", например, немного другая модель: они производят сырье, но не производят конечные продукты. И чтобы размещать свое сырье на внутреннем рынке, им приходится поддерживать переработчиков, запускать специальные программы, чтобы стимулировать переработку. Вы планируете в дальнейшем наращивать выпуск сырья, вы будете сами его перерабатывать или будете развивать и поддерживать перерабатывающие мощности в России, не только внутри Росатома, но где-то еще с партнерами, с другими компаниями, как вы это видите?
– У нас есть на сегодня две подобные модели, но они очень близки. И мы, скорее всего, будем реализовывать их параллельно. Конечно, станем наращивать переработку объемов сырья на мощностях, создаваемых для выпуска и углеродного волокна, и стекловолокна. Однако, мы также наработали хорошую практику партнерства с теми компаниями, которые занимаются переработкой.
Мы точно будем дальше поддерживать и развивать интеграцию за счет вовлечения в наш контур тех партнеров, которые уже создали производство по переработке материалов или по производству конечных изделий.
– То есть, по сути, будете формировать вокруг себя кластер партнеров, переработчиков, потребляющий ваше углеволокно?
– Да, когда это выгодно. Мы понимаем, что конкуренция должна оставаться, так как именно она мотивирует индустрию развиваться. Конечно, мы не будем всех скупать, но там, где это выгодно, мы будем стараться, не нарушая, естественно, общих рыночных правил.
Качество сырья
– Давайте поговорим о ПАН-прекурсоре. Насколько сейчас вы полностью обеспечены собственным сырьем для производства углеволокна?
– Мы имеем возможность выпускать тот объем ПАН-прекурсора, который бы полностью обеспечил производство углеродного волокна. Специфика отрасли такова, что переход с одного типа сырья на другой занимает время: в некоторых сферах квалификация неизбежно длится несколько лет. Мы не завершили переход на собственное сырье на 100% только по одной причине – продолжаются программы квалификации с нашими ключевыми партнерами.
– Отраслевые специалисты любят обсуждать углеволокно и Росатом, говоря о том, что сейчас качество сырья недостаточно высокое и не дотягивает до стандартов, что не позволяет выпускать, например, такие виды углеволокна, которые необходимы для производства баллонов компримированного газа. Так ли это? Когда планируется завершить все необходимые процедуры для перехода?
– Нет, это не так. Во-первых, мы на собственном ПАН-прекурсоре выпустили новый вид углеродного волокна UМТ-55, которое мы никогда не делали на иностранном прекурсоре. Волокно среднемодульное, с очень высокими характеристиками, оно очень востребовано, в том числе и в авиации. Мы не просто заместили один тип прекурсора на другой: наш собственный прекурсор не просто не хуже, а дал возможность разработать новый тип углеродного волокна, которого раньше не было никогда.
Во-вторых, те типы углеродных волокон, которые мы выпускали на иностранном прекурсоре, мы уже освоили на собственном, и свойства, которые мы получили в предсерийном режиме, оказались выше. Это подтверждено, статистически доказано, это не единичный результат, а система.
В-третьих, если говорить о баллонах высокого давления, то есть определенное противоречие между потребностями в баллонах определенного типа и тем волокном, которое для них требуется. Если мы говорим про баллоны четвертого типа, в которых нужно применять углеродное волокно или баллоны для водорода, которые должны выдерживать большое давление, то у нас есть волокно, из которого их можно делать. Вопрос здесь в том, какое волокно подойдет для того, чтобы выпускать баллоны в больших объемах с конкурентоспособной себестоимостью и ценой.
– Про технологии, уже касаемо выпуска сырья. Какая технология сополимеризации используется сейчас у вас на производстве сырья?
– Технология российская, мы занимались разработкой нескольких вариантов технологического оформления производства ПАН-прекурсора. Мы выбрали тот вариант, который нам подходит больше других, мы пришли к выводу, что выбранная технология не является фактором, ограничивающим предельные свойства углеродного волокна. Мы развивались в нескольких направлениях и несколько технологий довели до готовности к коммерческому применению, и по одной из них создали завод. Сейчас этот завод работает серийно, и то, что мы получили новый тип углеродного волокна с очень высокими характеристиками, подтверждает то, что мы сделали правильный выбор.
– И когда планируется завершить этот переход на полностью
собственное сырье?
– Программы квалификации будут длиться до конца 2025 года. Я думаю, что с 2026 года, если не появится новых изделий, которые потребуют такой длинной квалификации, мы уже будем близки к полному переходу на свой прекурсор.
– Ранее сообщалось, что планируется построить еще один завод по выпуску прекурсора аналогичной мощностью, как сейчас, но уже на другой площадке. Каков статус этого проекта, реализуете ли вы его, где будет построен завод?
– Разговор идет о масштабировании производств всех типов сырья, и углеродных волокон, и стекловолокон. Производство прекурсора нами не отделяется как самостоятельный проект, то есть если вопросы увеличения объема производства волокна потребуют еще одного ПАН-завода, то мы его построим.
Мы не привязаны ни технически, ни технологически, ни с точки зрения коммерции к какой-то одной площадке.
– То есть до какого-то конкретного обрамления пока еще проект по увеличению мощностей не дошел, правильно я понимаю? Площадка не выбрана?
– Мы еще не сделали окончательный выбор, поэтому ничего анонсировать не готовы.
Композиты необходимы
– Вы упомянули, что сейчас ваше производство зависимо от импортного оборудования, над российским вы работаете. Удастся ли реализовать планы по наращиванию мощностей с учетом текущей ситуации, доступно ли это оборудование в дружественных странах?
– Да, мы достаточно подробно изучили все эти вопросы, подготовились к реализации этих проектов. Я могу сказать, что мы способны увеличить объемы производства в несколько раз и оборудование для этого доступно. С учетом поддержки нашего проекта по замещению, по разработке собственного оборудования, я думаю, что мы с этим справимся.
– А можете ли назвать хотя бы срок, когда вы планируете принять инвестрешение о старте реализации проекта?
– Это зависит от слишком многих факторов, поскольку есть определенная процедура и правила утверждения инвестиций.
– В этом десятилетии?
– Да, с учетом ситуации, которая складывается на рынке, конечно, в этом.
– Ваш дивизион выпускает несколько типов углеволокна, есть ли какие-то уникальные типы, которые, допустим, в мире никто кроме вас не производит? Или, может, вы работаете над такими? В химии есть вещества, которые выпускаются условно по 100 г в год, но одним производителем в мире.
– У нас есть линейка высокомодульных углеродных волокон, в которых мы конкурируем с очень небольшим количеством производителей, а есть типы волокон, которые разрабатывались для специальных потребителей, где аналогов нет.
Мы находимся в России и можем модифицировать некоторые типы углеродных волокон так, чтобы они подходили к технологиям наших переработчиков лучшим образом, чем то, что они могут купить на рынке.
– А если говорить о продуктовой линейке последнего звена, как планируете ее расширять в дальнейшем?
– Сейчас в проработке у нас больше десяти проектов в области конечных изделий, где лидер по генерации новых применений — это строительство, поскольку и спектр заказчиков широкий и технические возможности компаний в нашем контуре широки. Мы в этом направлении с определенной регулярностью выпускаем новые продукты и точно будем продолжать.
Если говорить о продуктах, о которых мы еще не сообщали, но планируем разрабатывать, то у нас есть направление по автокомпонентам и мотокомпонентам. Мы эти изделия регулярно тестируем с нашими партнерами, выводим на рынок и в этой сфере тоже будем развиваться. Мы будем точно поддерживать развитие и тех сфер, которые уже начали развивать несколько лет назад — применение в спорте, в ветроэнергетике. Мы уже занимаемся баллонами высокого давления, будем продолжать ими заниматься.
– В основном профильном бизнесе Росатома, в ядерной энергетике, есть применение композитам на сегодняшний день?
– Есть две крупные области применения. Первое — это строительные решения на основе современных материалов, которые применяются при строительстве станции, и при восстановлении или создании инфраструктуры вокруг производств. Второе направление — часть оборудования, которое применяется в атомной энергетике, делается из композитов, где мы являемся поставщиком материалов.
– Можно ли привести практические примеры, как углеродное волокно повлияло на свойства того или иного материала, на КПД, технические характеристики, себестоимость?
– В некоторых ситуациях применение композитных решений просто необходимо, особенно там, где есть агрессивные среды и традиционные материалы, в отличие от композитных, подвергаются коррозии. И здесь мы видим затраты на эксплуатацию, ремонт и даже замену, которых может и не быть, если мы используем композиты.
Я бы хотел привести свежий пример – в начале этого месяца известный российский путешественник Фёдор Конюхов вместе с пилотом Игорем Потапкиным достигли Северного полюса. Причем тут композиты, спросите вы. Дело в том, что уникальный обтекатель двухместного мотопараплана изготовлен из угле- и стеклотканей нашего производства. Фёдор уже делал тренировочный полет в 2022 году, по итогам которого и было принято решение внести изменения в конструкцию, чтобы добавить обтекатель. Получилась прочная и легкая конструкция, позволяющую защитить пилотов от переохлаждения, а также был снижен вес и расход топлива.